How can we help your business?
[QSEA = QSENSE ENTRY ASSURANCE]
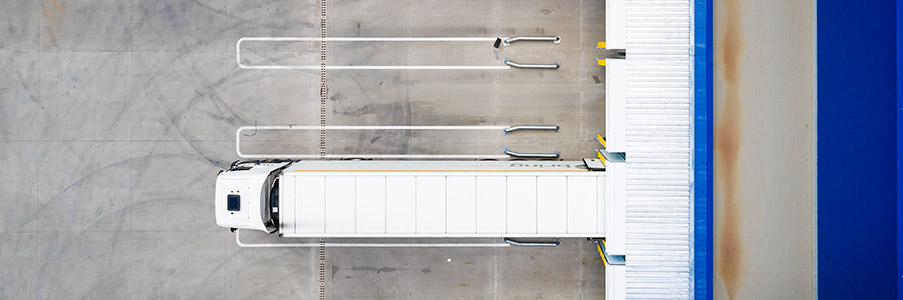
We eliminate non-conforming deliveries before commencing the production process. We prevent losses at later stages of production. We standardize quality requirements in a company with regard to suppliers and prepare a database which is verified in accordance with the adopted KPIs.
We take on the responsibility for qualitative and quantitative control of components and raw material before sending it to warehouses or production lines. This task is entrusted to a specialised SQA department (Supplier Quality Assurance) which is formed in your company and is where our engineers and quality controllers work. They control individual deliveries from your company’s suppliers, in accordance with the widely accepted/normative specifications (i.e. AQL) or in accordance with the specific requirements of the end client.
We accept the duty of contacting the suppliers and also undertake periodical evaluation. The results from the analysis, we communicate with a company’s Board of Directors.
FOR WHOM
For companies which receive components from external suppliers, work with new suppliers and are subject to a large number of faulty deliveries.
[QSDA = QSENSE DISPATCH ASSURANCE]
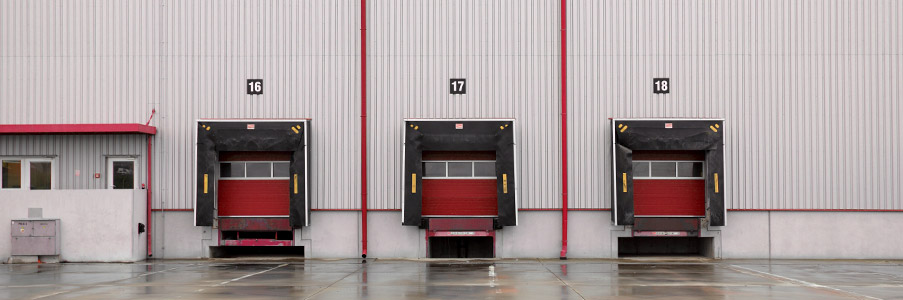
We implement the so-called Quality Wall, owing to which we can effectively evaluate and measure the parameters of a final product before it leaves your factory or warehouse.
We also improve communication between key departments in a company. As a result all workers involved in the production process gain access to knowledge, data and facts that influence the level of quality in a company and the speed of solving problems.
Qsense’s Quality Wall is a solution that enables visual and functional control and measurement of the final product before it leaves the factory. This is a characteristic measuring system that aims at detecting irregularities, which is continually validated, repeatable and reproducible and continuously improved and monitored. This is a flexible solution which is adapted to clients’ needs in terms of the scope of control and reporting.
The Wall also constitutes an element of knowledge management in a company. This is a communication centre in an organisation which integrates all information concerning quality, alerts and important messages for the staff, quality control manuals or undertaken actions, followed KPI characteristics.
As a result each employee that plays a role in a given process, receives support and can make decisions based on verified data.
The Quality Wall is implemented by professional QSense controllers who are covered by a training program and their qualifications are subject to continuous verification.
FOR WHOM
Practically for every manufacturing company which conducts quality control; in particular large factories where there is a need to streamline the communication and knowledge management processeses and most of all the stabilisation of new and unstable processes.
[QSPP = QSENSE PROCESS PERFECTION]
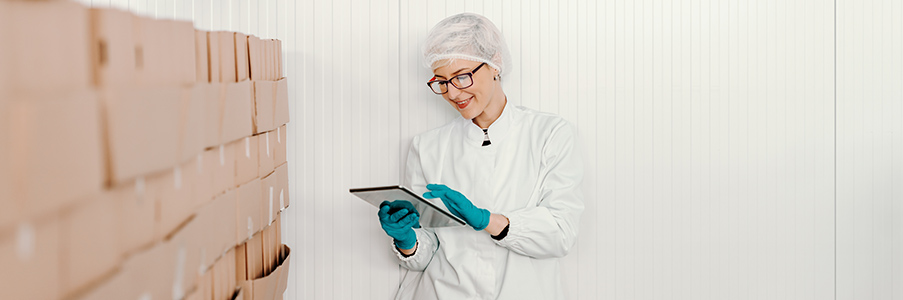
We undertake audits and the mapping of quality control processes in a company. We conduct problem diagnostics, from finding its sources to proposing corrective or preventative actions.
Within an audit we also take a close look at activities at different levels of production, logistics and deliveries. Analysis and audits are conducted in accordance to norms implemented in a company or in accordance to a specific client’s requirements, i.e. it could be VDA audits, FMEA analysis, 5S improvements and lean audits.
Taking advantage of our knowledge and experience of team members we analyse the collected results and present them to the client in a clear, readable and understandable way.
We prepare tailor made professional reports that are then presented to the final recipient.
Then, as per a client’s request, we implement corrective actions: we map out processes (VSM) or determine the requirements for any required improvements.
FOR WHOM
For companies which do not have the necessary recourses and knowledge so as to implement new processes or which struggle with recurring unconformity issues.
[QSCM = QSENSE CONTAINMENT MANAGEMENT]
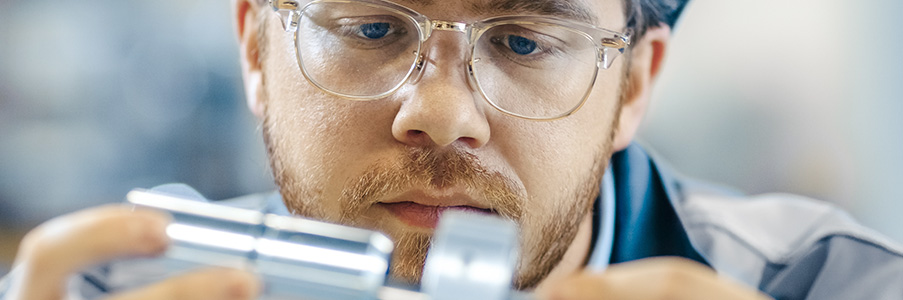
Component selection and corrective actions
We assure the continuity of the production process and prevent losses by obtaining only compatible components for production. We immediately exchange or repair faulty parts. We undertake control in accordance with the Controlled Shipment Standard on level 2 in a place chosen by the client.
As part of containment we carry out the selection of components necessary for production before commencing the production process. By applying the tested control methods (visual or by means of measuring equipment) we perform 100 percent of statistical check of all products in reference to any indicated quantitative or qualitative features. At the same time, we identify faulty or defective components and reject them before they enter the assembly line. Upon a client’s request we can repair them or arrange for an exchange.
This guarantees that the production process will not be interrupted, and the company won’t incur costs resulting from stoppage or future complaints.
This is an immediate action, easy to implement and also effective. As a result you receive a deep analysis of quality problems in your company and implementation of comprehensive and long-term corrective actions. It can be carried out as part of CSL1 and CSL2.
CONTROLLED SHIPPING – level 1 & 2 (CSL1 & CSL2)
We undertake control according to the Controlled Shipment Standard on level 2 in a place chosen by the client (at the supplier, in client’s a warehouse or any other agreed place).
Controlled Shipping is a particular standardized process which is run in a situation when a supplier delivered products non conforming with quality requirements. The whole process starts when the accepted number of irregularities or number of non-conforming products determined in a contract occur.
This process can be launched at two or even three levels, each being precisely defined and regulates responsibility on the line recipient – supplier.
Resident
We offer the possibility of delegating an experienced worker who would reside at your plant. This resident worker is present in the factory all the time and has the required knowledge concerning sudden events or faulty deliveries. As a result he/she can immediately undertake corrective actions and minimise the risk of production delays or complaints. The resident worker can undertake selection tasks or evaluate efficiency, and if necessary organise and manage an additional team of people.
FOR WHOM
For companies which need immediate solutions to faulty components deliveries, accepting deliveries from new suppliers or high risk deliveries, when stoppage or production delays is connected with high costs or lost benefits (i.e. situation of pressing deadlines for orders, which when exceeded can incur contractual penalties). Especially for the automotive industry.
[QSPP = QSENSE PROCESS PERFECTION]
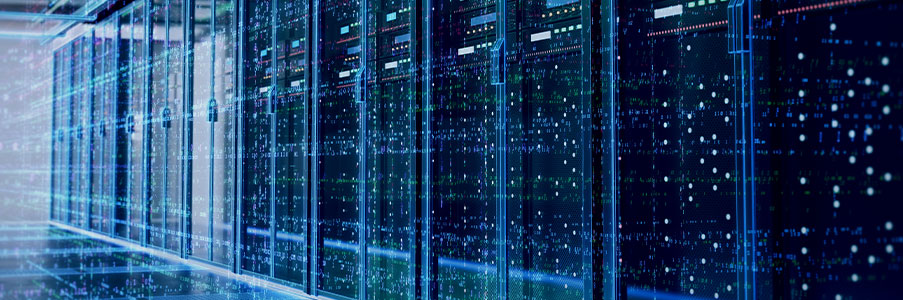
Depending on the customer’s needs, we supplement the control process with dedicated software elements. We can provide complementary solutions or the individual components needed to ensure the proper flow of data in the process.
Our standard procedure is based on the following steps. First, we cover integration with the customer’s systems. We load/capture data from external systems. Then we record measurements and inspection data. We create input forms with validation that are tailored to the process and products in question. Next, we take care of collection and protection in the form of databases, files or photo documentation of products. In the next step, we process these entities. We categorize, group and define relationships. We further deal with inference and determine the compatibility of the process and products. Having the above, we are able to create the appropriate report for the customer. Dynamically generated documents or dashboards, are fully customized. The customer receives insight into the data and reports through periodically sent files, or an online portal. We archive all data according to the client’s wishes and guidelines.
Our company is also involved in innovative technologies and solutions for employee training. We are developing applications of virtual reality, which make it possible to significantly increase the effectiveness of training and reduce its time. In times of limited mobility and increased need to maintain distance, these solutions find their applications very well.
The data extracted from the training of individuals allows us to identify the characteristics of the employee, making it possible to precisely define his competencies and tailor training to his individual needs. The areas we are currently working on in the context of VR training, in addition to quality control, are occupational health and safety.